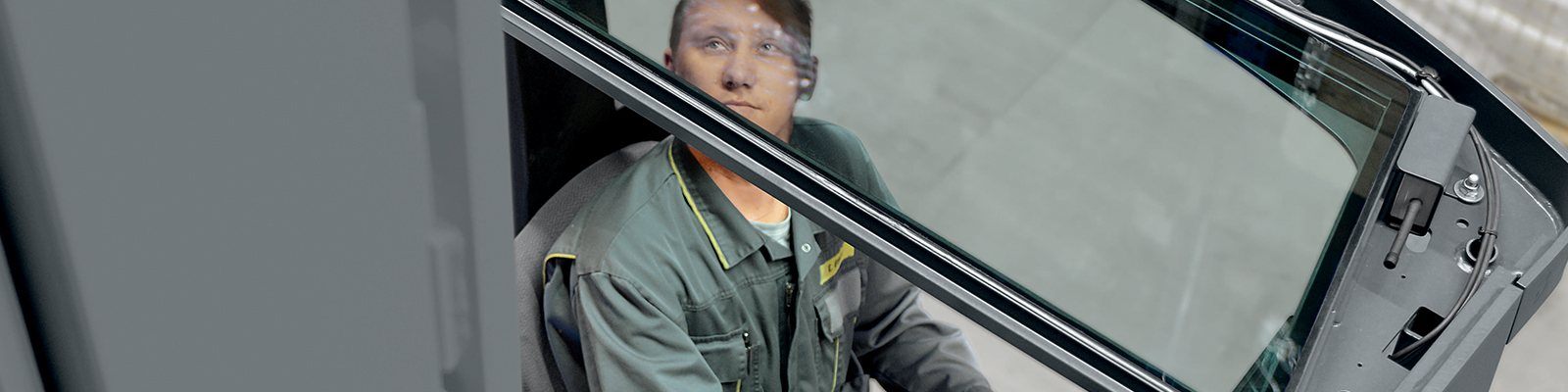
News
Why Convert to Electric Forklifts? Lower Total Cost of Ownership
“Clean energy” is a major focus for businesses large and small that want to prioritize better sustainability practices. In the material handling industry, electric forklifts are not just the future, they are already here making big inroads in warehouses and factories across the country. In fact, two thirds of all forklifts purchased in the US are electric.
To help your team make educated decisions about converting your fleet to electric, this three-part blog series will cover the reasons you might want to consider it. The series will cover these topics:
– The cost savings your business will realize as a result of using electric equipment.
– The environmental, business, health & safety advantages of electric forklifts.
– We’ll show you where incentives are available to offset the initial purchase investment.
Is having an electric fleet more expensive?
You may think converting to electric forklifts means an increase in cost, but that’s actually not the case long term. Perhaps the most compelling selling point of electric vehicles is lower total cost of ownership (TCO). While a larger investment is required up front when purchasing the units, your total spend over the life of the forklift will be less than what you’ll spend on an internal combustion (IC) forklift.
Fueling electric vehicles minimizes long-term costs
As we recover from the pandemic and reopen businesses, one of the first things we’ve seen as consumers is a sharp increase in the price of gasoline. Even when there isn’t a global health crisis affecting markets, fossil fuel costs generally fluctuate for a bevy of reasons, including the price of crude oil, seasonality, and supply & demand. With this market volatility, it is difficult to predict your fuel budget from year to year. Electricity prices, while subject to increases over time, do not fluctuate as greatly and historically have been very stable. Even if there were a percentage increase, the starting cost of electricity is so much less than fossil fuel that you’ll still be saving money.
Electric lift trucks have a longer lifespan than internal combustion lift trucks
The typical life cycle of an internal combustion forklift is about 12,000 hours. Electric lift trucks, however, generally average 15,000 hours. Depending on your usage, this could mean you get several more years of use of the unit.
Maintenance costs of electric forklifts are 15-20% lower
Because an internal combustion motor has more parts than an entire electric forklift, there is more to maintain and more that can go wrong. For example, with an electric lift truck, anti-freeze or oil systems are replaced by components that are simpler to maintain and have fewer moving parts. Fewer parts mean fewer breakdowns and fewer repairs, directly impacting your service calls and expenses.
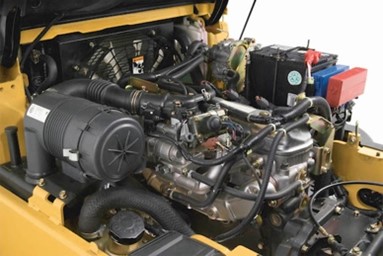
Internal combustion forklift motor
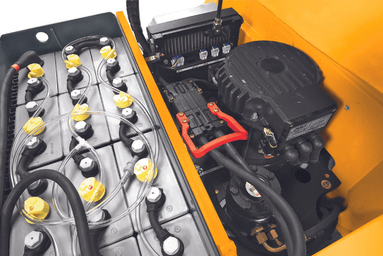
Electric forklift motor
Planned Maintenance service is important to have on any piece of equipment that gets regular use, and an electric forklift is no different. A PM on an electric truck includes checking status of battery, hydraulic system, steering system, etc. For electric these PMs might be cheaper.
Download our example ROI calculator to see a full breakdown of savings including acquisition costs, fuel costs, and a comparison of annual costs between the two engine types. In this example, our customer saves $82,000 over the span of five years with a fleet of 12 trucks.
If you’re interested in learning more about how to get started on an electric conversion initiative, contact us today.